12 Jan 2008
A Visit To Prespot Bamessing and Prescraft Bali
In Mid December 2007, I visited two of the three handicraft centers operated by the Presbyterian Church in Cameroon.
The idea of creating these centres was the brainchild of Swiss-cabinet maker and pastor Hans Knopfli. The first centers (now called Prescraft) were created in 1961 in Bafut and Bali Nyonga. Prespot situated at the foot of Sabga hill in Bamessing, was opened in 1983 to make clay-based products. Knopfli was a visionary and a man committed to the empowerment of the talented craftsmen he met during his missionary work in the 50’s in what is now called North West Province of Cameroon. According to a pamphlet obtained from Prescraft shop in Bamenda, “Prescraft and Prespot now provide outlets for some 700 craftsmen and women in the Cameroon Grasslands” to market their handicrafts.
The ABC of making pottery products at Bamessing
During our visit to the Prespot ‘factory’, the manager was absent but we were lucky to meet one of the able staff Nkono Linus that was kind enough to show us the different stages of molding a ceramic product. “There are 23 types of clay soil but only two types are used for pottery products”. He said, while showing us the area in the valley from where the clay they use is obtained. He explained that they do most of the clay digging in the dry season so as to take advantage to dry the clay.
The dug clay lumps are dried under shade. There are two types of clay (black and grey) that are usually mixed in the ratio of 3:1 to mold products. The partially dried lumps of clay blocks are beaten with sticks into small grainy particles. The particles are then dissolved in large drums of water, sieved to eliminate sand and other particles. The homogeneous paste is now put into cubical troughs made of clay block walls and metal for another round of drying. The drying process is completed by placing the paste further on flat surfaces of a rectangular board made from ‘plaster of paris’. The malleable clay paste is finally folded and wrapped with plastic sheets and stored for use in molding objects.
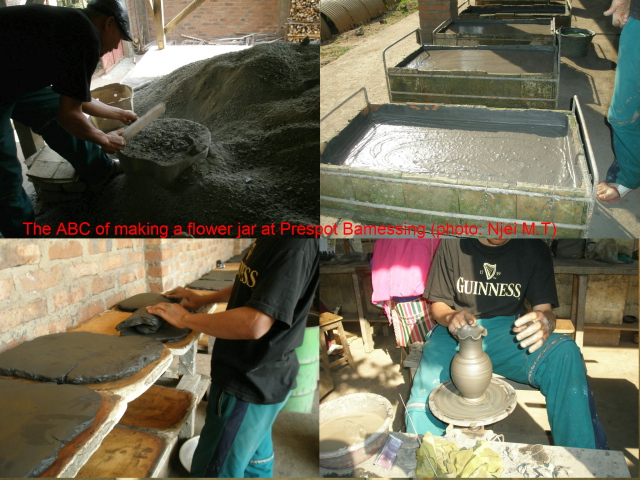
Explaining to us that only round objects are made on the potter’s wheel, Linus produced a flower jar in our presence to demonstrate how they mold objects. It was a very uplifting experience to see how he transformed a shapeless pile of clay into a beautiful flower jar in a couple of minutes. He explained that after molding, the product is left in the shade to dry for two weeks before heating it in the oven. The products usually pass through the oven twice. The first oven passage is called ‘biscuit firing’ in which the product is subjected to temperatures of 900-1000 degrees Centigrade for 10 to 11 hours. At the end of the biscuit firing, the dark brown material becomes reddish due to the effect of heat on Iron Oxide present in clay.
After the biscuit firing, the articles are left to cool down before applying glazing material on them. The glaze material is applied to make the product shiny and water proof. Glazing is akin to tablet coating in the pharmaceutical industry.
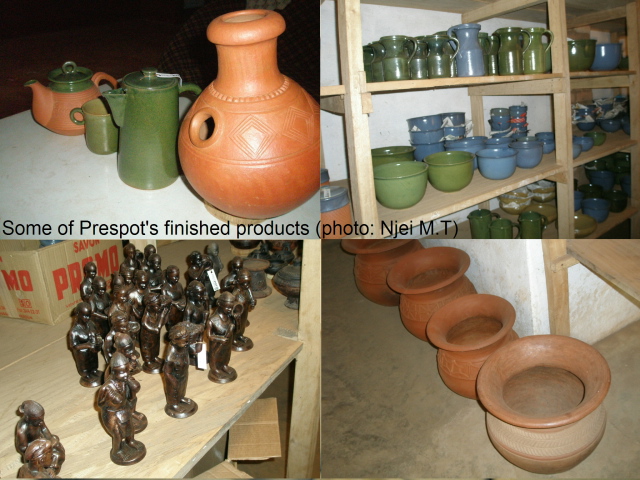
The glazed products are then subjected to even higher temperature (1100 Degrees C) for 24-28 hours.
The manufacturing process requires the use of large quantities of firewood to provide energy to the ovens (2.5 cubic meters for biscuit firing and about 5 cubic meters for glaze firing). The factory is surrounded by a large plantation of eucalyptus trees that supplies the firewood.
The Bali Handicraft Centre
Bali Nyonga is situated about 20 Kilometres on the outskirts of Bamenda. The Center in Bali comprises a carpentry workshop, carving, blacksmith, weaving, graphic arts, calabash decoration and knotting sections. I did see most of their products on display in their shop within the Centre complex. One of the long serving workers there Mbah Moses Godlove took me on a tour of the compound, explaining the different activities taking place at different sections. An array of products are produced by people supervised by this Centre and its sister centre in Bafut. These include baskets, bags, local musical instruments, furniture, toys and a host of other items.
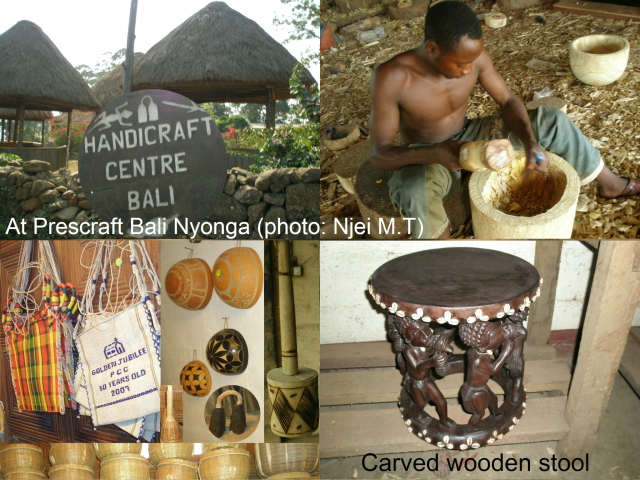
I also met with a former (Swiss) director of the Centre, Xavier Durig who came in from Switzerland for a brief visit. In my discussion with him, he gave me the impression that the Center was not performing up to expectation. He wondered aloud why Asian handicraft centres were evolving and perfecting the quality of their products while those in Cameroon were slow in innovations. According to him, the Centre should have been steadily growing but it advances in an up and down movement and apparently always needing the presence of expatriates to head it. It must be borne in mind that most of the objects sold by the centre are not made by people on its payroll. Craftsmen and women are ‘paid per piece’. It means that individuals operating independently make objects that meet the standards of the Centre and sell them to the Centre. Some use the facilities present at the Centre while others produce the objects at home.
Regardless of the shortcomings, it is evident that this part of the country still has talented people that can use their hands to create beautiful things.
Njei Moses Timah
|